5 Tips Trackless Machinery

When it comes to heavy-duty construction and industrial operations, trackless machinery has become an indispensable component. Unlike traditional tracked vehicles, trackless machinery offers enhanced versatility and mobility on various terrains, making it a preferred choice for numerous applications. However, to ensure optimal performance, safety, and durability of these machines, it's crucial to follow specific guidelines and best practices. In this article, we will delve into five critical tips for trackless machinery, providing insights into maintenance, operation, and strategic implementation.
Key Points
- Regular maintenance to prevent downtime and extend machine lifespan
- Proper operator training for safe and efficient operation
- Adaptive operational strategies for diverse terrain conditions
- Implementing a comprehensive safety protocol
- Strategic machine selection based on project requirements
Understanding Trackless Machinery
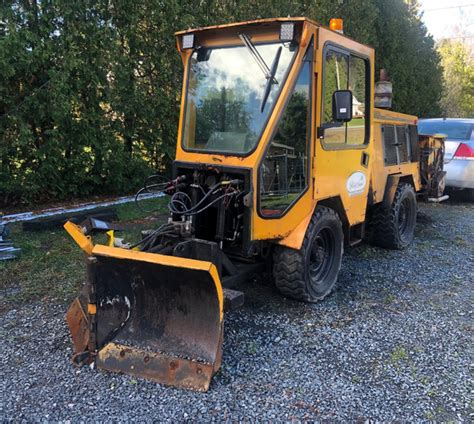
Trackless machinery encompasses a wide range of vehicles and equipment, including wheeled loaders, excavators, and dump trucks, designed for operations on hard surfaces or where tracked machines might not be feasible. The lack of tracks reduces ground pressure, allowing these machines to work on sensitive surfaces without causing damage. However, this also means they can be more susceptible to traction loss on uneven or slippery terrains. Understanding the capabilities and limitations of trackless machinery is fundamental to their effective and safe use.
Maintenance and Repair
Maintenance is key to the longevity and performance of trackless machinery. Regular checks on tire condition, fluid levels, and mechanical components can prevent unexpected breakdowns. For instance, a study by the Construction Equipment Association found that 60% of machinery downtime can be attributed to inadequate maintenance practices. Implementing a preventive maintenance schedule, including daily pre-operational checks and periodic deep maintenance sessions, can significantly reduce downtime and extend the machine’s lifespan. Moreover, having a spare parts inventory and a trained maintenance team on site can expedite repair processes when issues do arise.
Maintenance Activity | Frequency |
---|---|
Daily Pre-operational Checks | Before each use |
Fluid Level Checks | Weekly |
Tire Pressure and Condition Checks | Bi-weekly |
Deep Maintenance Sessions | Monthly |
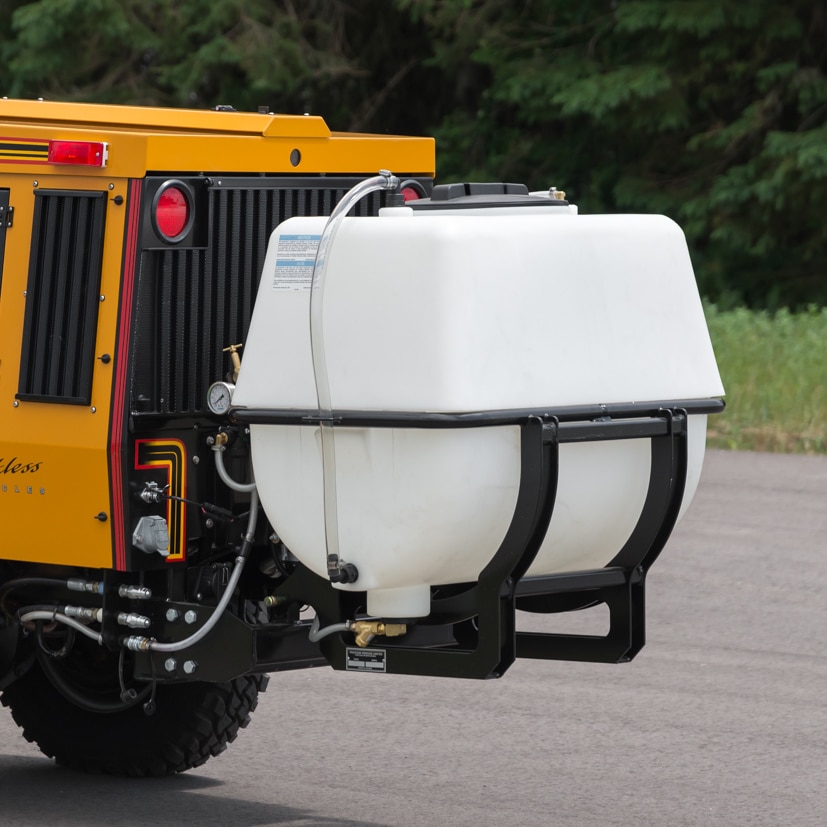
Operational Strategies
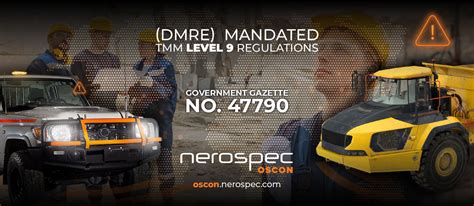
The operational efficiency of trackless machinery can be significantly enhanced by adopting adaptive strategies tailored to the specific terrain and project requirements. This includes adjusting speed according to surface conditions, utilizing the correct tire type for the terrain, and ensuring the machine is appropriately loaded to maintain stability. Furthermore, operators should be trained to recognize and respond to changing conditions, such as shifting from a paved road to an unpaved site, by adjusting their driving techniques accordingly.
Operator Training and Safety
Proper training of operators is paramount for the safe and efficient operation of trackless machinery. Operators should undergo comprehensive training that covers not only the operation of the machinery but also safety protocols, emergency procedures, and terrain adaptation techniques. A case study by the Occupational Safety and Health Administration (OSHA) highlighted that operators who received thorough training experienced a 40% reduction in accidents related to machinery operation. Additionally, implementing a strict safety protocol, including the use of personal protective equipment (PPE), regular safety briefings, and a culture of safety awareness, can minimize risks associated with machinery operation.
What are the primary considerations for selecting trackless machinery for a project?
+The selection of trackless machinery should be based on the specific requirements of the project, including the type of terrain, the weight and volume of materials to be handled, and the desired operational speed and efficiency. Additionally, considerations such as fuel efficiency, maintenance costs, and operator comfort should also be taken into account.
How often should trackless machinery undergo maintenance checks?
+Maintenance checks for trackless machinery should be conducted regularly, with the frequency depending on the usage and operational conditions. Daily pre-operational checks, weekly fluid level checks, and monthly deep maintenance sessions are recommended to ensure the machinery remains in good working condition.
In conclusion, the effective use of trackless machinery in construction and industrial operations hinges on a combination of regular maintenance, proper operator training, adaptive operational strategies, comprehensive safety protocols, and strategic machine selection. By adhering to these guidelines and best practices, operators and project managers can ensure the safe, efficient, and productive use of trackless machinery, ultimately contributing to the success of their projects.